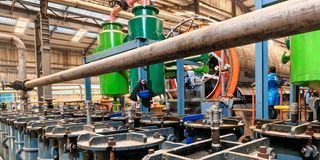
Inside West Valley Sugar Company factory on June 13, 2025. The factory has modern systems aimed at revitalising sugar production in western Kenya.
Standing at the porch of the factory as our bodies are bathed by steam from a massive water recycling pit below, Mr Alfred Soi, the chairman of West Valley Sugar Company, points towards an unfinished structure that looks like a sub-station and raises his voice above the roar of the mills.
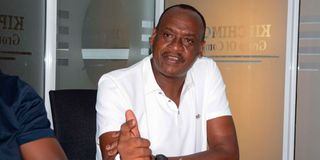
Alfred Soi, the chairperson of West Valley Sugar.
“We are building our own distillery,” the company chairman says.
West Valley is not even three years old but appears like it is running before it can even crawl. The ambition is paying off.
The new miller has leased Muhoroni Sugar – one of the country’s oldest sugar factories – a paradox that is not lost on Kisumu Governor Anyang Nyong’o.
West Valley’s distillery, whose details are still scant, will be used to make ethanol from molasses, a thick brown syrup that is left when sugar crystalises.
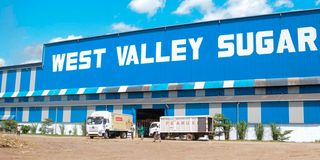
West Valley Sugar Company,
The distillery will also get molasses from Muhoroni Sugar Company in Kisumu County.
Kipchimchim Group of Companies, which owns West Valley, is building another sugar factory in Trans Mara, Narok County, which will be its other source of molasses.
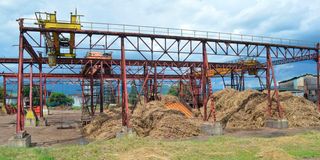
Cane yard at Muhoroni Sugar Company.
Apart from ethanol, sugarcane can also be used to make other products.
A classic illustration of squeezing many valuable products from cane is offered by Kibos Sugar and Allied Industries.
Kibos is also based in Muhoroni Sub-County, Kisumu. It is one of the key players in the industry, crushing 804,873 tonnes of cane in 2023, according to official statistics.
The Kibos Complex has plants for milling, power generation, a sugar refinery, a distillery, a paper mill and fertiliser-making.
To achieve all these, one needs tens of thousands of acres of sugarcane. The investor also requires efficient mills.
That is why the leasing of Chemelil Sugar Factory and the nucleus farm – also in Kisumu County – is important for Kibos, which is owned by the Chatthe family.
When the cane is crushed, the dry pulp that is left – also known as bagasse – is pushed into the boilers where it is heated.
This, in turn, heats water whose steam is eventually used to make electricity to power the factory and plant.
This method of producing electricity is known as bagasse co-generation.
With adequate electricity due to a good supply of sugarcane, the miller can produce surplus electricity which can then be sold to the national grid.
This was the game plan of Mumias Sugar’s 35MW bagasse-based co-generation plant that saw it sign an agreement with Kenya Power to supply the distributor with electricity.
However, the plan was disrupted when the company ran out of bagasse due to a reduced supply of cane.
The low-lying fruit for most of the new sugar barons is the manufacture of ethanol – a sector dominated by Agro Chemical and Food Company Ltd, a government-owned distillery.
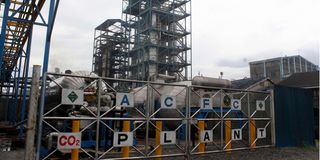
Agro Chemical & food Company Limited in Kisumu County.
In raw form, molasses can be used to improve animal feed or make fertiliser, but it is largely transformed into ethanol, which is then used in the distillation of spirits like whiskey, gin or rum by compounders.
The Rai Group, which has an iron grip control over refined sugar through its five subsidiaries, has set its eyes on the cane by-products, particularly electricity co-generation and ethanol production.
Rai Group’s subsidiary – West Kenya Sugar Company – is soon building a Sh3.86 billion distillery next to its sugar factory in Kakamega that has a milling capacity of 5,000 tonnes of cane per day (TCD).
With the leasing of Bungoma-based Nzoia Sugar Company which has a TCD of 3,000 for the next 30 years, West Kenya will barely run short of molasses to supply its distillery that is designed for making extra neutral alcohol (ENA), fusel oil and technical alcohol for 330 days a year.
As long as all the plants in the five subsidiaries under Rai Sukari – the holding company for the Rai family sugar factories – keep humming, cane will be milled and molasses will be produced.
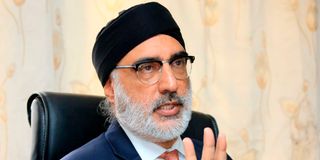
West Kenya Sugar Chairman Jaswant Singh Rai.
Mr Jaswant Rai, the chairperson of Rai Group who not very long ago appeared to be at loggerheads with President William Ruto, was controversially handed by the Head of State Mumias Sugar Company’s electricity co-generation and distillery plants.
Read: How Ruto cornered sugar baron in pitched battle to control struggling miller
This decision has been opposed by the area leaders and residents. Analysts say it is a move that is likely to inflame the rivalry between Mr Jaswant and his brother Sarbjit Rai of Uganda’s Sarrai Group .
Sarrai Group is running the factory under a lease granted by receivers appointed by the KCB Bank.
It is still not clear if West Kenya will be paying for the molasses from Mumias.
On the Nandi Hills-Kimwani road in Nandi County, the family of Brig (rtd) Peter Kipchirchir Magut, is setting up Tiryo Sugar Mills Limited at an estimated cost of Sh357.8 million.
Apart from a sugar miller with a daily crushing capacity of 1,000 tonnes, the Eldoret-based investor is also building a 45 kilolitre per day distillery as more entrepreneurs plunge into the alcohol business.
Could Agro-Chemical Ltd, which gets 80 per cent of its molasses from some of these sugar millers, be worried about the new competition?
“The market is huge,” says Mr Edwin Owino, the General Manager in charge of Finance and ICT at Agro Chemical.
Portable spirits produced by leading alcohol manufacturers like the East African Breweries Limited (EABL), London Distillers or Kenya Wine Agencies Limited are valued at Sh200 billion and give the taxman about Sh18 billion in excise duty every year.
EABL, which is listed on the Nairobi Securities Exchange, gets most of its ethanol from Agro Chemicals Ltd, but the company management says it is never enough.
The alcohol manufacturer is usually forced to look for more ethanol from elsewhere to plug the deficit.
“When the companies modernise the mills, their capacity will go up,” says Mr Owino, adding that this will see them produce adequate sugar for the local market.
When sugar production goes up, he adds, molasses will also increase, with the distilleries having more than they require.
He says this is the reason Agro Chemical imports molasses from distilleries in Uganda, which also happen to have mills.
Manufacture of cosmetics
“It is a mill but is able to sell extra. One company cannot produce everything,” Mr Owino adds.
Ethanol can also be denatured, or made unfit for human consumption. Such can be used for the manufacture of cosmetics and pharmaceuticals.
Besides bottled spirits, Agro-Chemical Ltd manufactures baker’s yeast, hand sanitiser and carbon dioxide.
Unlike most of the state-owned sugar companies whose inefficiencies led them to struggle to even get enough sugarcane and venture into making other products, the new mills are keen to get the most out of the white gold.
Dr Jane Pamela Odhiambo, the incoming Managing Director of New South Nyanza Sugar Company (Sony) 2025, says as part of the long-term project, the private investor plans to diversify into many by-products of sugar processing.
“There are areas the company was hoping to get into for a long time, including electricity co-generation and producing ethanol,” Dr Odhiambo says.
In countries like Brazil, refined sugar can be a by-product. The South American nation produces more than enough for domestic consumption.
When he made a presentation before the National Assembly Committees of Finance and Agriculture, Mumias Sugar Company General Manager Rakesh Bvats warned against taking this route.
“It should be made clear to millers that sugar is their first priority. The by-products come after,” Mr Rakesh told the lawmakers.
That is not surprising. There is a high demand for table sugar, which the local market has not been able to meet. That makes the country import the deficit.
Mr Owino urges caution as the millers diversify. He says the companies should not make the mistake of Mumias Sugar, “which went into many things at once, including areas it had no experience”.
“If I were these people putting up the new mills, I would first revamp the factories and invest in cane development. That will take about five years,” he says.
Read also: