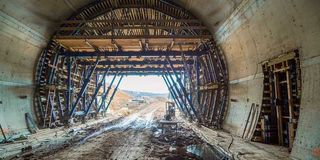
Over the past decade, developers in Nairobi have leveraged modern technology such as tunnel and aluminium formwork widely, to deliver major real estate projects within a short timeline without compromising on quality.
Due to their price limitations, these technologies have, however, not been very popular in smaller towns away from the city, where developers have preferred to work with conventional forms of construction. As the demand for housing in these towns has increased, driven primarily by a growing youthful population, the use of modern construction technologies has however begun to make more economic sense to developers beyond Nairobi.
“Through formwork technology, a developer can deliver a housing unit within a year and pass the cost savings to homeowners while maintaining quality workmanship,” said John Mwaura, CEO of Finsco Africa Limited, in an interview with DN2 Property.
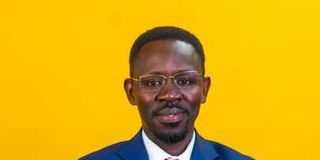
John Mwaura CEO of Finsco Africa.
Aluminium Formwork is a construction model that involves the use of lightweight reusable aluminium panels to allow for the simultaneous casting of walls, slabs, beams and other structural elements. As for tunnel formwork, it uses reusable forms to create monolithic concrete walls and slabs, often in a single, continuous pour, making it ideal for projects with repetitive cellular construction, such as residential blocks, hotels, and student accommodation.
The overall cost per square foot of aluminium formwork is much less compared to other conventional types of formwork materials due to the high reusability factor.
The erection process can be executed even by an unskilled labour force, without incurring high costs of hoisting cranes or lifting equipment. Finsco Africa has been leveraging the technology to put up a 1,600-unit residential project near Thika town dubbed Thika Grove Chania.
“Aluminium formwork is able to produce high quality concrete surfaces, precise dimensions and a smooth surface finish, minimising the need for extensive plastering or remedial work,” stated Mwaura.
This not only guarantees durability, environmental sustainability and high accuracy in finishing, but also helps to reduce labour cost, which brings down the overall cost of construction. Leveraging the same technology, Finsco Africa plans to expand its housing portfolio to other towns such as Machakos, Kiambu, Murang'a, Kisumu, Eldoret, and Nakuru, where the demand for housing has been increasing.
“Land in these towns is generally cheaper than Nairobi, therefore although the initial cost of deploying the aluminium form is high, we are able to still deliver affordable units in these areas,” posed Mwaura.
Just as modern technologies have transformed operations in several industries, significantly improving efficiency and convenience, John says that these technologies can also revolutionise the construction industry.
“When the Covid-19 pandemic struck, we saw how prefabrication or modular construction helped strained facilities develop units that would accommodate the growing number of patients,” noted Mwaura.
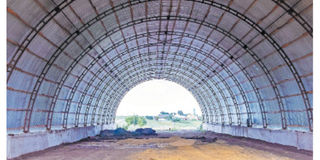
Prefabrication involves manufacturing building components off-site in a factory and then transporting them to the construction site for assembly. It offers advantages such as increased efficiency, reduced waste, a lower carbon footprint, improved quality control and reduced cost.
“The Kenyan construction industry is picking up with the trends of technology, however, the uptake is still low, especially at the construction stage on sites,” remarked Mwaura.
Through policy interventions, the developer says that there is a need for the government to support the adoption of technologies that can help to address the current housing deficit.
For example, 3D volumetric construction, which involves creating complete three-dimensional building sections in a factory setting, which can be transported to the site for assembly, can help reduce construction timelines.
“This system also requires fewer on-site workers and can be completed in any weather conditions, which is why it’s effective for projects with tight deadlines or those with labor shortages,” explained Mwaura.
It is almost similar to pre-engineered or precast flat panel systems, which involve the off-site production of floor and wall units before being transported to the construction site for assembly. This ensures that each panel is designed precisely to speed installation.
“Projects that once took months can now be completed in weeks without sacrificing quality or durability. This construction technique is particularly advantageous for projects involving repetitive designs, such as residential complexes and commercial buildings,” stated Mwaura.
Others such as precast concrete foundations, offer the advantage of speed and reliability. Unlike traditional poured foundations, precast foundations are manufactured in a controlled environment, ensuring consistent quality.
The technology also reduces adverse weather's impact on the construction schedule, making it ideal for regions prone to extreme weather conditions, as it allows for a more predictable construction timeline and superior durability. Meanwhile, flat slab construction, which involves using thick, reinforced concrete slabs supported directly by concrete columns without beams, can be ideal for commercial and retail buildings.
“When coupled with Building Information Modelling (BIM) technologies and artificial intelligence tools, these modern construction technologies become an interesting way to lower the cost of construction,” said Mwaura.
Although the upfront cost of these modern construction technologies is high, Chris Ochieng’, CEO of Gulf Cap Real Estate, says that the benefits they generate far outweigh the costs.
Not only do they help reduce wastages on site and shorten construction timelines, but they also empower construction professionals to enhance collaboration, improve efficiency and meet the demands of complex construction projects.
“An apartment floor that could take several weeks or months to complete, could for instance be completed within a week,” says Ochieng’.
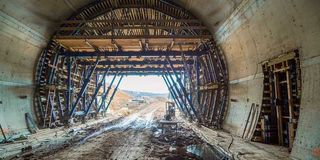
Since the time taken to do a project with these technologies is significantly reduced, developers incur lesser costs during construction, and this cost-benefit can then be transferred to the consumer.
“A project that would take up to five years to complete, like one that we are currently working on in Starehe dubbed 289 InCity Suites, could be completed within two years,” remarked Ochieng’.
Unlike traditional forms, which are not very good for the environment, many of the modern construction technologies focus on sustainability and therefore help to reduce energy consumption, operating and maintenance costs as well as reduce carbon emissions. This makes the property more appealing to customers who are willing to pay premium rates for access to projects that were constructed using sustainable building practices.
“Buildings are a major contributor to climate change. They consume a lot of resources in their construction in the form of materials used and the embodied energy necessary for their execution. Environmentally conscious technologies help create greener buildings,” posed Ochieng’.
In addition to improved marketability, developers stand to benefit from funding from financial institutions that tend to give preferential treatment to developers who adhere to sustainable building practices.
“Sustainable projects enable real estate developers to access finance via instruments such as green bonds that are subject to tax incentives and lower interest rates,” said Michael Mathenge, an architect and the Secretary of AAK Architects Chapter.
These bonds not only provide developers with access to suitable financial products for profitable construction but also enhance a company's reputation as a socially responsible organisation. Sustainable building technologies also safeguard the property from devaluation over time, ensuring that even those who inherit the property get to benefit from good rental yields and capital gains.
“When you uphold the leasehold value of a property, investors will certainly be attracted to it because they know they can generate value for an extended period of time,” stated Mathenge.
On the downside, Brenda Nyawara, the Vice President of the Architectural Association of Kenya, says that while durable, modern technologies such as aluminium forms can be dented or damaged if not handled carefully, which may affect their longevity and reusability.
“Aluminium panels are easily capable of suffering dents and deformation which makes them less durable within drops or improper handling. To mitigate risk, proper storage and skilled labor is required to ensure the system lasts over time,” posed Nyawara.
Additionally, the assembly and disassembly of aluminium formwork can be noisier compared to other forms such as timber, which in essence reverses the other environmental benefits it has. The assembly and disassembly of aluminium formwork may also require skilled labour, which can increase labour costs if workers are not already trained.
“Labor efficiency does remain quite efficient but initial training and expert supervision are prerequisites during the first few instances to ensure that the correct installation and stripping is achieved,” said Nyawara.
Modern technologies such as aluminium formworks also have high thermal conductivity, which may affect the curing process of concrete in extreme temperatures unless properly managed.
While the technology is great for standard shapes and dimensions, it may not be as flexible as other materials for custom or complex designs. Construction using the technology can only start after detailed planning. After a formwork system has been constructed, changes on-site become complicated.
“Customised changes during the construction timeline can lead to expensive and tedious processes to create or adjust new panels. Additionally, costs and timelines may spiral out of control if there is any last-minute architecture or structural work done,” noted Nyawara.
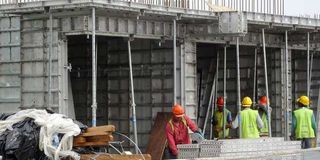
Nairobi developers are increasingly using tunnel and aluminium formwork to quickly build high-quality real estate projects.
That notwithstanding, with a housing deficit of over 200, 000 units a year, modern technologies such as tunnel and aluminium forms may be the solution that the country needs to meet its annual housing demand. However, as they are fairly new in the country, few local artisans can effectively use them in construction. In order to increase usage, John Mwaura, CEO of Finsco Africa, says that investing in professional development and upskilling of staff, through benchmarking and information sharing, is key.
“You can only implement what you know, so if you do not travel out there to understand how people are using these technologies, then you can never be able to apply the same here,” stated Mwaura.
Professional development can also help to curb accidents which could occur from handling the formwork materials when workers, particularly those who are inexperienced, use machines and equipment or handle heavy and large materials without proper training.
“Workers’ safety is greatly dependent on proper information, instruction, training, and supervision. Staff must be informed and trained, so that they understand the nature of risks to their health and safety from the work they do,” said Mwaura.
The developer however says that the most effective way of achieving a high level of safety when using the formwork technology is to have reliable supervision during erection and concrete pouring, to ensure that workers follow the instructions and training given to them.
“Supervisors must ensure that the formwork delivered is manufactured as per the client’s design, to ensure safety during installation as well as avoid wasting time,” noted Mwaura.